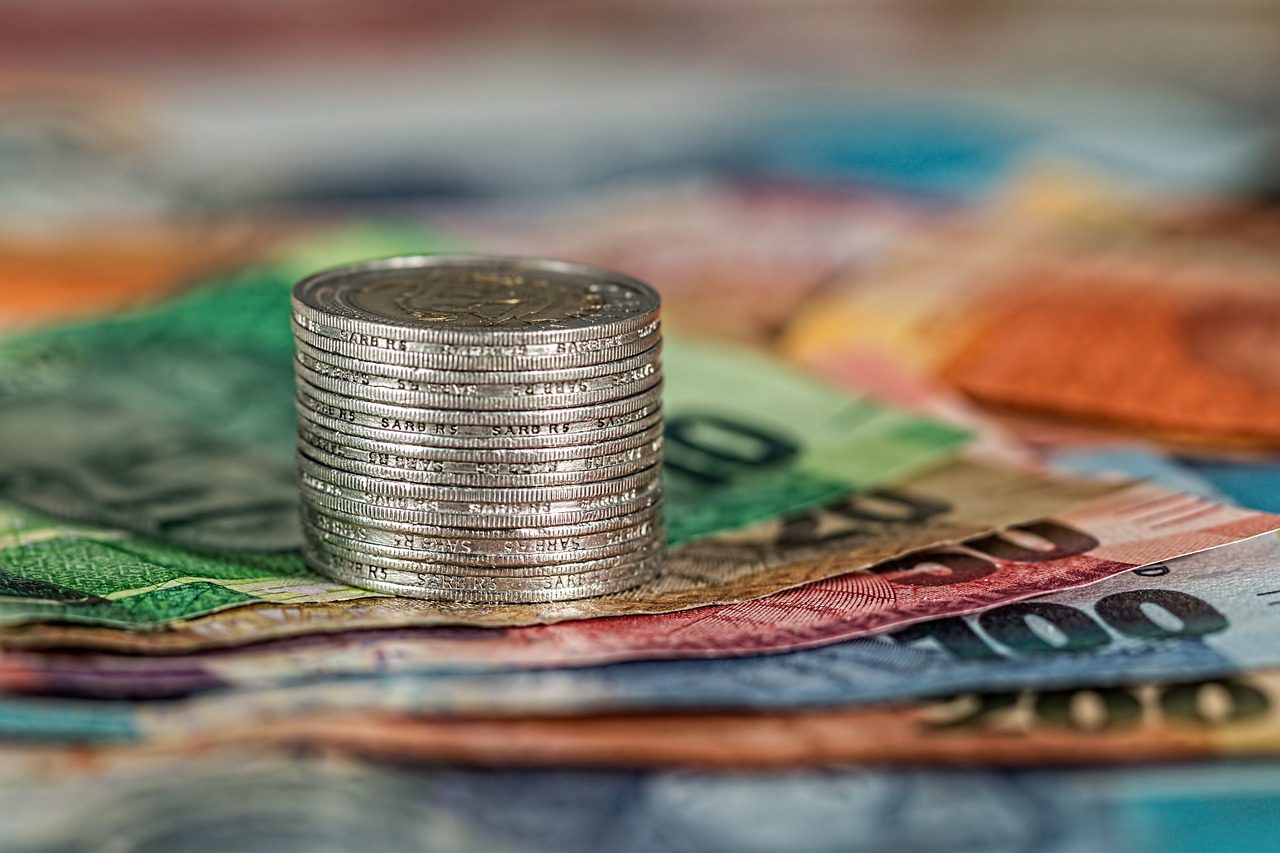
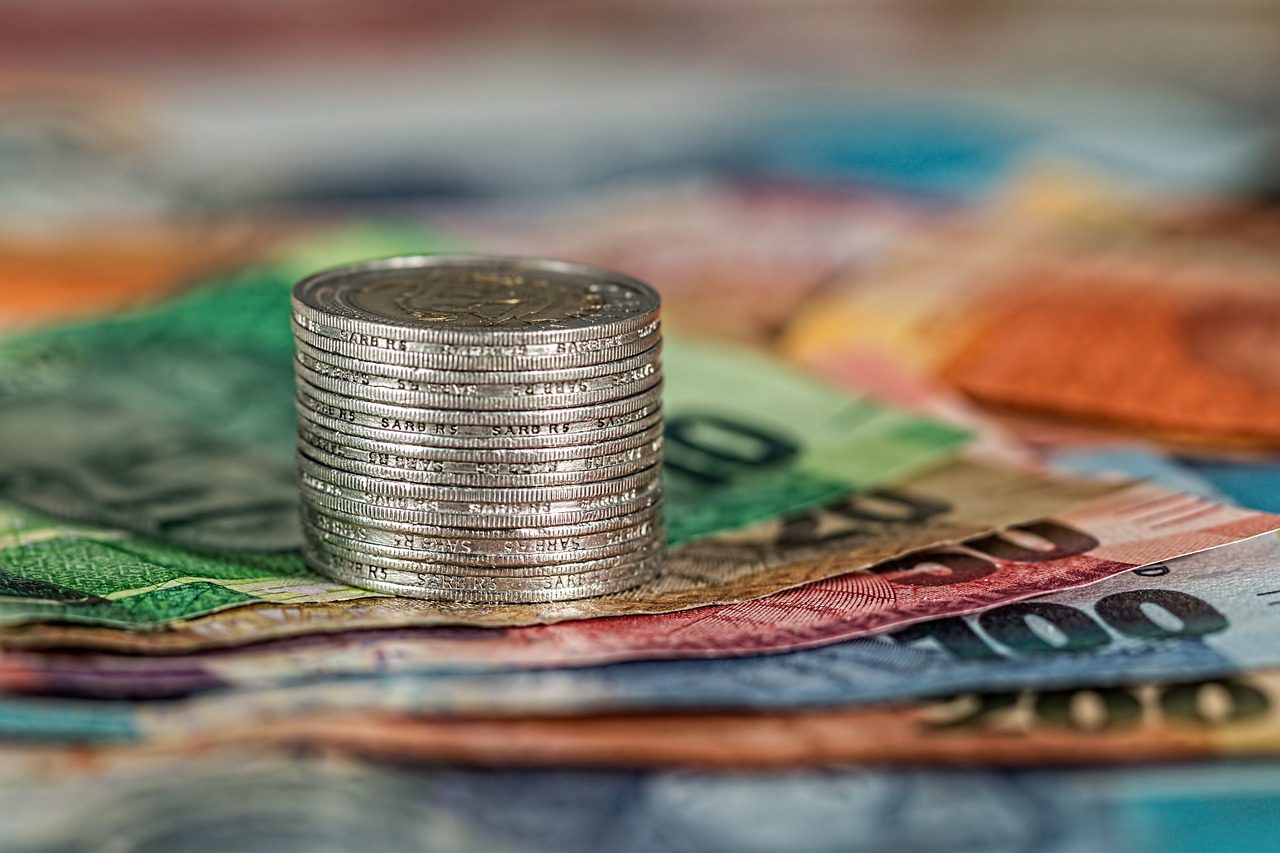
How to reduce the cost of securing?
How can you reduce docking costs ?
Is it possible to reduce costs while maintaining or increasing the performance of your lashing systems?
We often hear that tie-downs are too expensive. This belief leads companies to invest little in securing equipment and training. However, the lack of interest in good lashing practices also deprives companies of the knowledge they need to minimize costs through the proper use of lashings.
Finally, we believe that responder safety should never be dependent on economic constraints…
On what technical aspects can a company reduce its costs ?
Increase friction factor.
When using top-over lashing (otherwise known as friction lashing), the friction factor is crucial. This stowage method is mainly used for road transport. It aims to increase friction between the loading surface and the load.
The performance of this technique depends on several factors:
– Strap tensioning force
– Lashing angle.
– The friction factor.
-Good tension distribution (gliding corners).
We’re going to focus on the friction factor, because modifying it drastically reduces the number of straps required.
Other factors are also taken into account, such as whether or not the load is blocked against the transport vehicle’s surroundings. For our examples, we’ll consider that the load is not blocked in order to appreciate the differences in influencing the friction factor.
First example:
Let’s take the case of a 10,000 kg wooden crate loaded on a flatbed trailer (wood-on-wood support). The load is not blocked against the front apron.
The straps used are fitted with long-grip tensioners (STF 580 daN). Vertical lashing angles are 80°.
In this configuration, 18 straps are required to secure the load in compliance with NF EN 12195-1.
Second example:
We take the above parameters and modify the friction factor by adding an anti-slip mat credited with a friction factor of 0.6.
In this configuration, only 4 straps are required to secure the load in compliance with NF EN 12195-1.
Comments :
We can see from the examples above that the friction factor has a significant impact on the number of straps, reducing the number of pieces of equipment required by more than a factor of 4.
a) Utiliser la bonne technique de sanglage : recourir à un arrimage direct quand cela est nécessaire.
Strapping technique is also extremely important, as it directly impacts the number of straps.
Not knowing the fundamental difference between friction and direct lashing will cause major problems, with the risk of making insufficient lashings that can cause damage.
A strap placed in a head loop can offer a holding force of 4,000 daN or more, depending on the type of strap (much more than a strap used for friction lashing).
“Not knowing the fundamental difference between friction lashing and direct lashing will cause major problems with the risk of making insufficient lashings.”
Utiliser convenablement les entourages résistants des engins de transport.
Another frequently observed error is the failure to make proper use of the blocking capacity of the walls of transport equipment. We’ll take a few examples to explain what we mean.
Mixed loading in a container :
In this case, we take a load of 10,000 Kg made up of loads of different dimensions. As the loading plan had not been studied beforehand, the loader loaded with empty spaces at the doors. It positions crossbars between the container’s solid flutes to secure loads, or a bastaing (10cm x 5cm) capable of providing a holding force of 750 daN (often seen). You’d need several of them to secure the load properly.
Solution:
Revisit the loading plan to take up all the floor space and, above all, use the doors to retain the loads. The blocking capacity of a container’s front wall and doors corresponds to 40% of the payload. This means that a container with a payload of 28,000 kg will have a locking capacity (doors or front wall) of 11,200 daN.
This is far superior to the strength of nailed wooden wedges or crossbars set into the grooves of container walls. Empty spaces can also be filled with dunnage or empty pallets.
Once again, a good understanding of lashing techniques enables us to anticipate loading and use appropriate means, providing the minimum number of lashing devices.
Bonne connaissance des points d’arrimage sur les semi-remorques.
Another cost-saving factor is the correct use of lashing points on semi-trailers. This is particularly true for loads of heavy parcels or concentrated loads requiring direct lashing with straps or chains.
Standard EN 1260 states that the permissible tensile strength (load limit) of the lashing points depends on the gross vehicle weight. For vehicles whose gross weight exceeds 12,000 kg, the permissible tensile force of the lashing points must be at least 2,000 daN. What does this mean in relation to the use of tie-downs for such a vehicle ?
This means there’s no need for 6,000 daN mooring chains or other devices with a holding force greater than 2,000 daN. In fact, we have very often found that a lack of knowledge of the strength of lashing points on carriers has resulted in an inappropriate choice of lashings with too great a holding force, which will not be fully utilized.
The strength of a complete lashing system (e.g. : lashing point on machine, webbing, lashing point on cargo) will be limited to the weakest element.
Costs can therefore be reduced by correctly sizing the strength of the lashings in relation to the load to be secured, while taking care to respect the capacities of the transport equipment. This is a very common mistake.
The above list of examples is not exhaustive. There are many subtleties depending on the loads to be secured. Our aim is to raise awareness among loaders, carriers and all other companies involved in securing loads. During our audits, we make every effort to recommend the most appropriate practices, while keeping costs under control for the beneficiary companies.
Related posts
Loading dangerous goods (IMDG)
The transport of dangerous goods is governed by the IMDG code for maritime shipm
Loading and securing responsibilities in road transport.
Do shippers really know what their responsibilities are? It’s not uncommon
Statistics on non-conformities in the transport of dangerous goods
NCB statistics (2019 survey). A recent study uncovers a worrying safety problem